Fiberglass, also known as FRP, GRP, a composite material made from fine glass fibers embedded in a polymer matrix, has revolutionized industries worldwide since its commercialization in the 1930s. Combining the strength of glass with the flexibility of plastics, it offers a unique blend of properties that make it indispensable in applications ranging from aerospace to consumer goods. This article explores fiberglass’s composition, manufacturing processes, key products, intrinsic properties, and its transformative role across diverse industries.
1. Introduction to Fiberglass
What is Fiberglass?
Fiberglass, or glass-reinforced plastic (GRP), is a composite material consisting of glass fibers (typically 3–25 microns in diameter) bound together by a thermosetting resin, such as polyester, epoxy, or vinyl ester. The glass fibers provide tensile strength and rigidity, while the resin matrix distributes loads and protects the fibers from environmental damage.
Historical Development
- 1930s: Owens-Illinois and Corning Glass Works developed the first commercial glass fibers.
- 1940s: Widespread adoption in World War II for radar domes and aircraft components.
- 1950s–Present: Expanded into construction, automotive, and renewable energy sectors.
Manufacturing Process
- Fiber Production:
- Melting: Silica sand, limestone, and soda ash are melted at 1,400–1,600°C.
- Fiber Drawing: Molten glass is extruded through platinum bushings to form continuous filaments.
- Sizing: Fibers are coated with lubricants and binders to enhance adhesion to resins.
- Composite Formation:
- Layup: Fibers are woven into mats, fabrics, or rovings and impregnated with resin.
- Curing: The resin hardens via heat, pressure, or catalysts, forming a rigid structure.
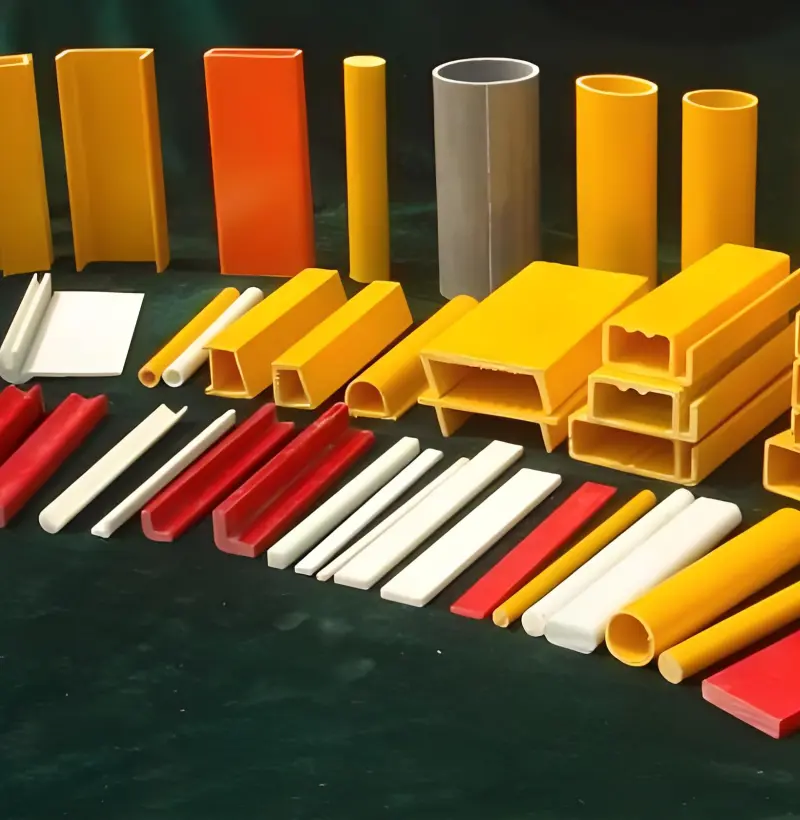
FRP Profiles
2. Key Fiberglass Products
Fiberglass is engineered into diverse forms to meet specific industrial needs:
Product Type | Description | Applications |
---|---|---|
Fiberglass Roving | Untwisted bundles of parallel filaments | Pultruded profiles, filament winding |
Woven Fabrics | Fibers interlaced in bidirectional patterns | Boat hulls, wind turbine blades |
Chopped Strand Mat | Randomly oriented short fibers bonded with resin | Automotive panels, bathtubs |
Fiberglass Pipes | Cylindrical structures with corrosion-resistant lining | Chemical processing, water treatment |
Insulation Wool | Lightweight, fluffy material for thermal/acoustic insulation | Buildings, HVAC systems |
Reinforced Thermoplastics | Fiberglass blended with plastics (e.g., PP, PA) | Electrical enclosures, consumer goods |
Molded FRP Grating | Grid-like panels formed by molding resin and fibers | Industrial walkways, offshore platforms |
Covered FRP Grating | Molded grating with anti-slip surface coatings | Stair treads, chemical plant flooring |
FRP Rod | Solid cylindrical profiles | Concrete reinforcement, fishing rods |
FRP Pultruded Tube | Hollow tubes made via continuous pultrusion | Structural supports, electrical conduits |
FRP H Beam | I-beam profiles for high-load structures | Bridge girders, warehouse frameworks |
FRP U Channel | U-shaped structural sections | Edging, cable management systems |
FRP Angle | L-shaped profiles for corner reinforcement | Tower braces, machinery frames |
3. Properties of Fiberglass
Fiberglass’s popularity stems from its exceptional physical, chemical, and mechanical properties:
A. Mechanical Properties
- High Strength-to-Weight Ratio: Tensile strength of 1,000–3,000 MPa (comparable to steel) at 25% of steel’s density (2.5 g/cm³ vs. 7.8 g/cm³).
- Stiffness: Elastic modulus of 70–85 GPa, ideal for load-bearing structures.
- Fatigue Resistance: Withstands cyclic loading without cracking, critical for automotive parts.
B. Thermal and Electrical Properties
- Thermal Insulation: Thermal conductivity of 0.03–0.05 W/m·K, outperforming most metals.
- Fire Resistance: Non-combustible up to 540°C, with low smoke emission.
- Electrical Insulation: Dielectric strength of 10–20 kV/mm, suitable for electrical components.
C. Chemical and Environmental Resistance
- Corrosion Immunity: Resists acids, alkalis, and saltwater, unlike metals.
- UV Stability: UV-resistant resins (e.g., isophthalic polyester) prevent degradation in sunlight.
- Low Moisture Absorption: <0.1% water absorption, preventing swelling or warping.
D. Design Flexibility
- Can be molded into complex shapes, colored, or textured during production.
4. Industry Applications
Fiberglass’s adaptability has made it a cornerstone material in multiple sectors:
A. Construction and Infrastructure
- Structural Panels: Lightweight wall panels and roofing sheets reduce building costs.
- FRP Structural Profiles: FRP H Beams, U Channels, and Angles replace steel in corrosive environments (e.g., coastal bridges, chemical plants).
- Walkway Systems: Molded FRP Grating and Covered FRP Grating provide slip-resistant, durable surfaces for industrial platforms and pedestrian bridges.
B. Automotive and Transportation
- Body Components: Hoods, bumpers, and fenders reduce vehicle weight, improving fuel efficiency.
- Aerospace: Radomes, interior panels, and cargo liners leverage fiberglass’s strength and radar transparency.
- Railways: FRP Pultruded Tubes and Rods are used in overhead cable supports and lightweight seating frames.
C. Marine and Offshore
- Boat Hulls: Fiberglass-reinforced polyester resists osmotic blistering and marine fouling.
- Decking: Molded FRP Grating withstands saltwater corrosion on ship decks and oil rigs.
D. Energy and Utilities
- Wind Turbines: Fiberglass-epoxy composites form lightweight, durable blades up to 100 meters long.
- Electrical Grids: FRP Pultruded Tubes serve as non-conductive crossarms in high-voltage transmission towers.
E. Industrial and Chemical
- Support Structures: FRP H Beams and Angles frame chemical storage tanks and scrubbers.
- Cable Trays: FRP U Channels organize wiring in corrosive industrial settings.
5. Advantages Over Traditional Materials
Material | Key Limitations | Fiberglass Advantages |
---|---|---|
Steel | Prone to corrosion, heavy | Lightweight, corrosion-resistant |
Aluminum | Lower strength, higher cost | Higher strength-to-weight ratio |
Wood | Susceptible to rot, pests, and fire | Durable, fire-retardant |
Concrete | Brittle, requires reinforcement | Flexible, crack-resistant |
6. Innovations and Sustainability Trends
- Recyclable Resins: Development of thermoplastic composites (e.g., PA6-GF) for easier recycling.
- Pultrusion Efficiency: Automated production of FRP Pultruded Tubes and H Beams reduces material waste.
- Bio-Based Fibers: Hybrid composites combining glass fibers with natural fibers (flax, hemp).
The global fiberglass market, valued at $12.8 billion in 2023, is projected to grow at 5.4% CAGR, driven by green construction and electric vehicle adoption.
7. Challenges and Future Prospects
- Health Concerns: Inhalation of glass dust during manufacturing requires stringent safety protocols.
- End-of-Life Management: Recycling FRP Angle and Grating remains technically challenging but critical for sustainability.
Future advancements may include:
- Smart Fiberglass: Sensors embedded in FRP Pultruded Tubes for structural health monitoring.
- Hybrid Systems: Combining FRP H Beams with carbon fiber for ultra-high-strength frameworks.
Conclusion
Fiberglass stands as a testament to material science’s ability to bridge the gap between nature’s limitations and human ingenuity. From Molded FRP Grating securing industrial walkways to FRP Pultruded Tubes revolutionizing energy infrastructure, its versatility continues to redefine engineering possibilities. As industries prioritize sustainability and performance, fiberglass will remain a vital enabler of innovation, proving that even the most unassuming materials can shape the future.
WeChat
Scan the QR Code with WeChat