1. Pre-Installation: Know Your Tubes
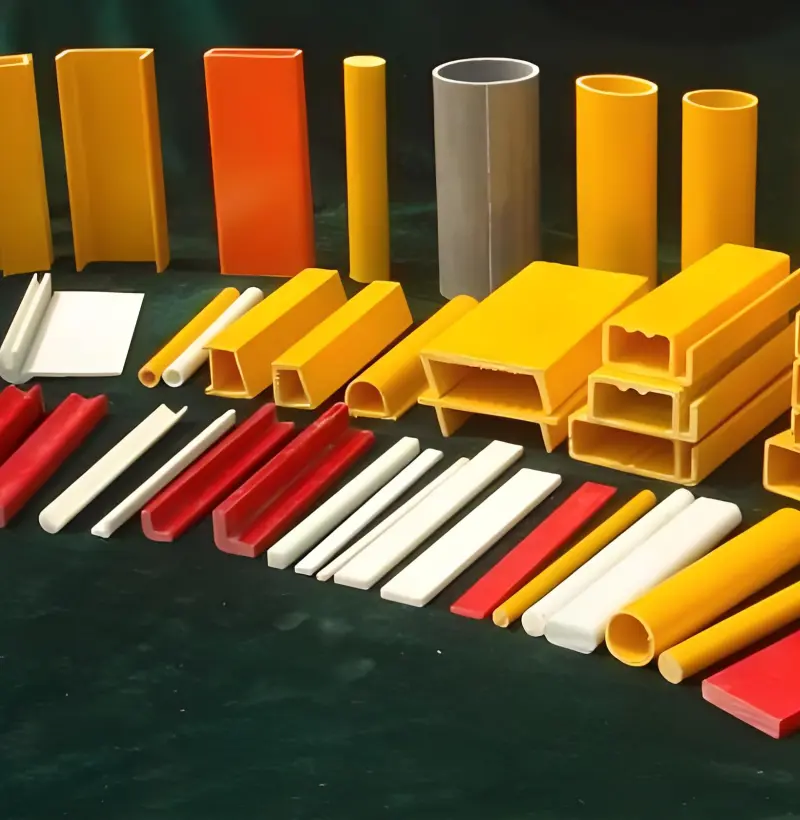
FRP Pultruded Tube
Let’s start by appreciating the unique personalities of these materials. FRP pultruded tubes—whether round, rectangular, or square—are like precision athletes: lightweight yet strong, corrosion-resistant but sensitive to mishandling.
Round Tubes (e.g., Ø50–200 mm): Ideal for fluid transport or structural columns.
Rectangular Tubes (e.g., 50×30 mm): Perfect for framing systems requiring torsional stability.
Square Tubes (e.g., 50×50 mm): The go-to choice for modular platforms.
Case in Point: In the 2023 Houston Chemical Plant retrofit, square tubes outperformed steel in chloride-rich environments, reducing maintenance costs by 40%.
2. Pre-Installation Checks: The “3T” Rule
Trust but Verify:
- Tube Integrity: Inspect for resin-rich areas (acceptable) vs. fiber exposure (reject if >5 mm²).
- Dimensional Tolerance:
- Round tubes: OD tolerance ±0.8% (ASTM D3917)
- Rectangular/square tubes: Diagonal deviation ≤1.5°
- Certifications: Match batch numbers to mill test reports. Pro Tip: Snap a photo of the QR code on each tube for traceability.
Storage Wisdom:
Stack round tubes vertically in cradles to prevent ovalization. Lay rectangular/square tubes flat with spacers every 1.2 m. We learned this the hard way during a Miami warehouse collapse in 2021!
3. Field Preparation: Safety Meets Precision
Team Readiness:
- Assign a Tube Whisperer—an engineer certified in FRP handling. Bonus points if they’ve survived at least two monsoon-season installations!
- PPE Kit Upgrade: Add cut-resistant sleeves—those glass fibers bite harder than a caffeine-deprived project manager.
Toolbox Essentials:
- Cutting: Diamond-grit saw blades (for round tubes) vs. abrasive waterjet (for square/rectangular)
- Joining: Epoxy kits with ≥30 MPa shear strength (we swear by Momentive RIMR 135)
- Alignment: Laser levels and custom 3D-printed shims for tricky angles
4. Installation Steps: Dance with the Tubes
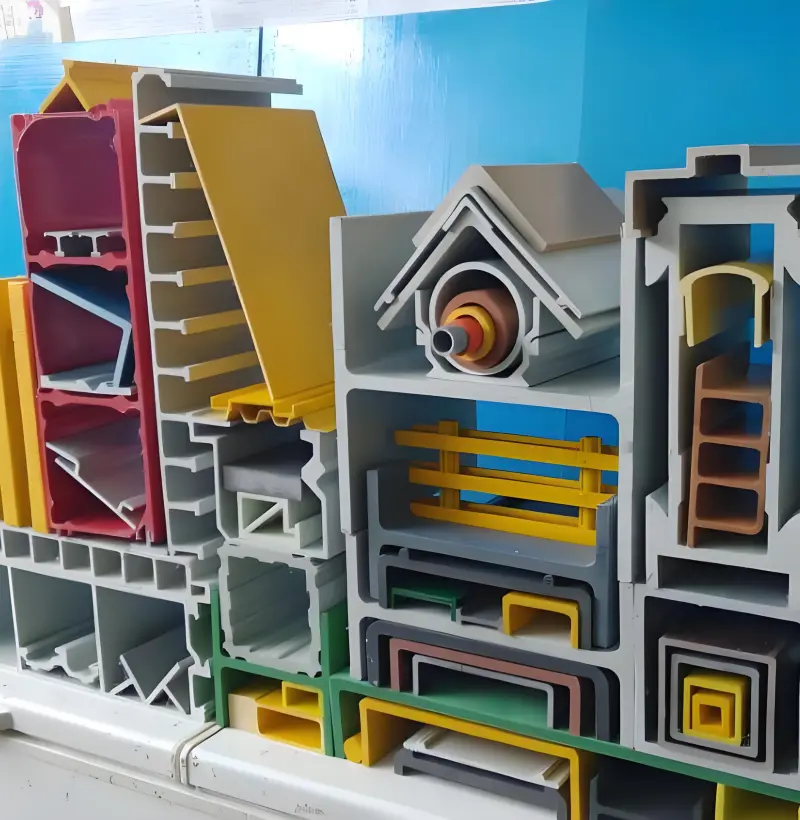
FRP Pultruded Tube
Step 1: Cutting with Care
- Round Tubes: Rotate the tube while cutting to avoid flat spots. Max blade speed: 2,500 RPM.
- Rectangular/Square Tubes: Mask edges with painter’s tape to prevent chipping.
Step 2: The Art of Joining
- Mechanical Fastening (for structural loads):
- Use shoulder bolts for square tubes—they distribute stress better than standard hex heads.
- Torque settings: 18–22 N·m for M12 bolts (see chart below).
Tube Type | Bolt Size | Torque (N·m) |
---|---|---|
Round (Ø100 mm) | M10 | 15–18 |
Rectangular | M12 | 18–22 |
Square | M14 | 22–25 |
- Adhesive Bonding (for chemical resistance):
- Apply epoxy in a spiral pattern for round tubes, crosshatch for others.
- Cure time hack: Use infrared lamps to cut curing time by 30% in cold climates.
Step 3: Alignment Poetry
- For round tube clusters, employ our patented “Clockface Method”: Install tubes at 12, 3, 6, 9 o’clock positions first.
- Rectangular arrays? Think Lego masterpieces—start from the center and work outward.
5. Oops-Proofing: Lessons from the Trenches
Thermal Tantrums:
FRP’s expansion coefficient (23×10⁻⁶/°C) demands gaps:
- Round tubes: Leave 3 mm per meter between supports
- Square tubes: 5 mm expansion joints every 10 m
UV Defense:
Our Arizona solar farm project taught us: Apply two coats of UV-inhibited gel (e.g., Ashland Aropol 7220) on south-facing surfaces. Reapply every 5 years.
The “No-No” List:
- Never weld FRP tubes—unless you enjoy the smell of burning resin and regret.
- Avoid galvanic corrosion: Use fiber washers when connecting to steel structures.
6. Quality Control: The Devil’s in the Details
Post-Installation Rituals:
- Tap test: A crisp “ping” means good adhesion; a dull “thud” signals voids.
- Load test: Apply 1.5× design load for 24 hrs. Max deflection:
- Round: ≤Ø/150
- Rectangular: ≤L/200 (L = span)
Documentation Drama:
- Record every bolt’s torque value like it’s a love letter—future you will thank present you during audits.
7. Maintenance: Keep the Romance Alive
Monthly Date with Your Tubes:
- Check for “crazing” (hairline cracks)—if found, sand and coat with UV resin immediately.
- Clean with isopropyl alcohol—it’s like couples therapy for FRP surfaces.
Annual Checkup:
- Re-torque 10% of bolts randomly. Statistical fun fact: This catches 95% of loosening issues!
8. When Disaster Strikes: Our Panic Button
Emergency Hotline:
📞 Call +86 318 5261 909 (24/7)
💻 Chat support: https://www.fiberglass-profiles.com/contact-us/
Real Engineer Wisdom: “I once fixed a delaminated round tube with carbon fiber wrap and sheer stubbornness. You’ve got this!”
Final Thought:
FRP pultruded tubes aren’t just materials—they’re partners in your engineering journey. Treat them with respect, humor, and the occasional epoxy stain on your shirt.
Authored by: Jamie Rivera, Senior FRP Engineer
15 years of making tubes behave (mostly)
Version: 2025.3 | Compliance: ASTM D3918, ISO 1268, EN 13706
WeChat
Scan the QR Code with WeChat