At our company, we take pride in engineering FRP structural tubes that redefine strength, durability, and corrosion resistance. Whether you’re in civil engineering, marine construction, or industrial infrastructure, our structural fiberglass tubes provide a superior alternative to traditional steel and aluminum.
Key Applications
Our FRP structural tubes excel in:
- Bridge & Infrastructure Support – Lightweight yet high-load-bearing capacity.
- Marine & Offshore Platforms – Immune to saltwater corrosion, reducing maintenance costs.
- Chemical Processing Plants – Resistant to acids, alkalis, and harsh industrial environments.
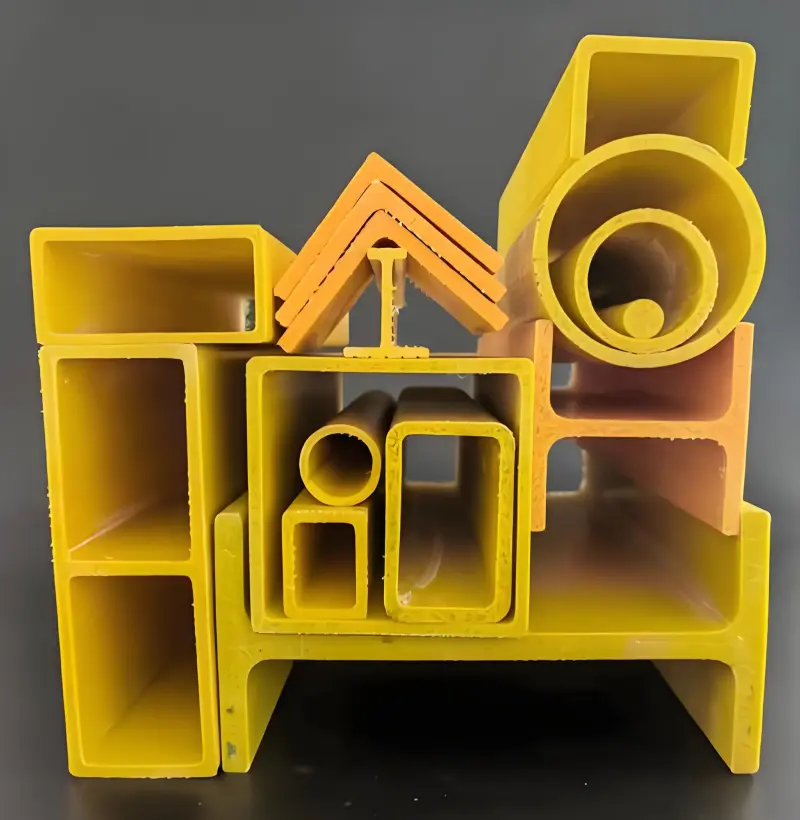
FRP Structural Tube
Product Specifications
- Material: High-grade fiberglass reinforced polymer (FRP)
- Diameter Range: 50mm – 500mm (custom sizes available)
- Wall Thickness: 3mm – 20mm (adjustable for load requirements)
- Tensile Strength: 300-700 MPa (surpasses mild steel in strength-to-weight ratio)
- Thermal Stability: -40°C to +120°C
Why Choose Our Structural Fiberglass Tubes?
✔ Corrosion-Free – No rust, even in extreme environments.
✔ Lightweight – 75% lighter than steel, reducing installation labor.
✔ Non-Conductive – Safe for electrical-sensitive applications.
✔ Long Lifespan – 50+ years with minimal maintenance.
Proven Performance & Industry Trust
Our FRP structural tubes are rigorously tested per ASTM D3916 and ISO 9001 standards. Leading engineering firms and government agencies rely on our products for critical infrastructure projects.
Real-World Success Stories
- Offshore Wind Farm Support Structures – A major European energy company replaced steel with our structural fiberglass tubes, cutting maintenance costs by 60%.
- Wastewater Treatment Plant Walkways – A U.S. municipal project used our tubes to eliminate corrosion issues, extending service life beyond 30 years.
Installation & Replacement
Our structural fiberglass tubes are designed for easy retrofitting. Unlike steel, they don’t require welding—simple mechanical fasteners or adhesives suffice. Replacement is rare, but if needed, modular designs allow quick swaps without full system shutdowns.
Maintenance Tips
- Inspect annually for surface abrasions (though internal integrity remains unaffected).
- Clean with mild detergent—no special coatings needed.
- Avoid extreme impact (while tough, intentional heavy strikes can cause localized damage).
Critical Considerations
- UV Exposure: For outdoor use, we recommend a UV-resistant gel coat (optional).
- Thermal Expansion: Slightly higher than steel—account for this in large-span installations.
Expert Insights
From our 20+ years in FRP manufacturing, we’ve learned:
- Proper joint design is crucial—use our engineering support for optimal load distribution.
- Avoid galvanic corrosion when connecting to metals—use insulating spacers.
FAQs
Q: How do FRP structural tubes compare to steel in cost?
A: Initial cost is higher, but lifetime savings (no corrosion, minimal maintenance) make them 30-50% cheaper long-term.
Q: Can they be painted or coated?
A: Yes, but rarely needed—gel coat colors are factory-applied for lasting aesthetics.
Innovation & R&D Commitment
We continuously invest in advanced pultrusion techniques and nanocomposite enhancements to push the limits of structural fiberglass tubes. Recent breakthroughs include:
- Self-monitoring smart tubes with embedded strain sensors (patent-pending).
- Hybrid carbon-FRP tubes for aerospace-grade strength.
WeChat
Scan the QR Code with WeChat